- 4/3 direct operated solenoid controlled directional valve with an electromagnetic mechanical detent on the control spool, specifically designed for steering mode selection.
- Zero power consumption during two wheel steering mode.
- Control spool with positive overlapping to reduce leakage and switching shocks.
- Stand-alone zinc plated valve housing with threaded ports and fixing holes for direct line mounting.
- Wet pin solenoid tubes for DC coils, with inherent push rod for mechanical override on the control spool; zinc plated.
- Standard coil connections available in DIN and DEUTSCH (additional connections on request).
- Size 6
- Series 00
- Maximum operating pressure 210 bar (3046 psi)
- Maximum peak pressure 230 bar (3336 psi)
- Maximum flow 50 l/min (13.2 gpm)
- Ports G 3/8 - G1/2 - SAE 8

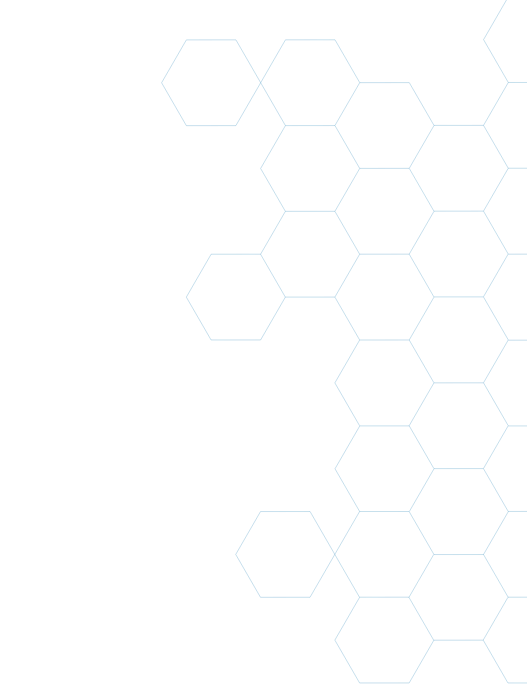
Compact Directional Valves - Stand-alone 4-way directional valves - Steering mode selection
SMV2
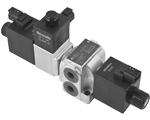
General specifications
Ordering details
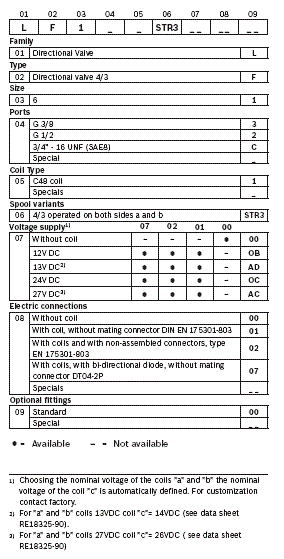
Functional description
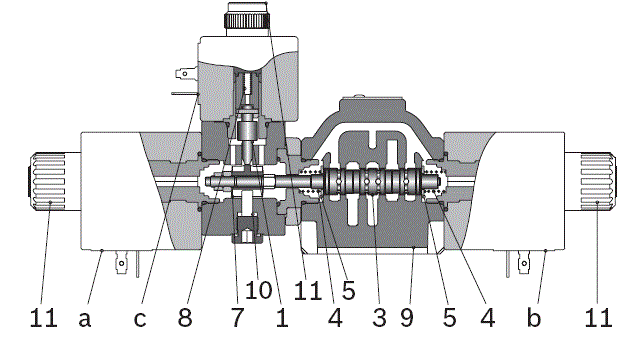
The SMV2.0 directional control valves with electromagnetically actuated mechanical detent are used for selecting between three steering modes.
In the de-energized condition, the control spool (3) is held in the center position by return springs (4); the spring (8) pushes the detent pin(1) against the bushing (7). In this condition the valve is in the front steering configuration (2WS) as all of the coils are de-energized.
In order to switch the steering mode (see pictures below), it is necessary to first actuate the mechanical detent by energizing the coil “c” in order to allow the control spool to move.
Then, by energizing one of the coils “a” or “b”, the control spool switches from the center position (2WS) to a different steering mode, 4WS-A or 4WS-B.
When a 4WS mode is selected, the control spool coil, “a” or “b”, must continue to be energized during machine operation; it is also necessary to de-energize the coil “c” to lock the mechanical detent into position. The mechanical interference between the bushing (7) and the detent pin(1) locks the control spool and prevents unwanted movements generated from external agents. (i.e. short circuit on the coils “a” or “b”).
The return springs guarantee the return to the center position by pushing on the washer (5) that is against the control spool.
Spool variants
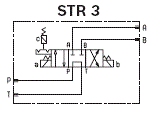
All wheel steering 4WS-A
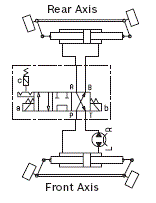
Front steering 2WS
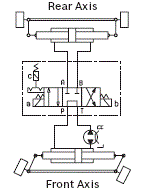
Crab steering 4WS-B
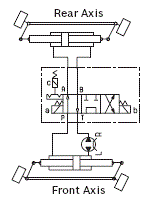
Logical sequence of Operation
The following shows the logical sequence of operation that guarantees the valve operates correctly.
2WS: two wheel steering
4WS-A: four wheel steering (turn).
4WS-B: four wheel steering (crab).
The switching times in the table above are measured on test benches at defined hydraulic conditions (ISO6403). The operating conditions can significantly affect switching times. For this reason it is suggested to increase them as necessary.
Technical data
For further information on the coil “c”, see data sheet RE18325-90 (coils S8-356 - CLASS H 20W). Coils with connector type DEUTSCH DT04-2P include, as standard, a bidirectional diode.
Below is a list of the standard coil “c” model codes:
General
- 2.23 kg (4.92 lbs)
- Unrestricted
- –20....+50 (-4....+122) (NBR seals)
- 150 years see RE 18350-51
Hydraulic
- 230 bar (3336 psi)
- 250 bar (3625 psi)
- 210 bar (3046 psi)
- 230 bar (3336 psi)
- 50 l/min (13.2 gpm)
- Mineral oil based hydraulic fluids HL (DIN 51524 part 1). For use of environmentally acceptable fluids (vegetable or polyglycol base) please consult us.
- –20....+80°C (-4....+176°F) (NBR seals)
- ISO 4572: βₓ≥75 X=12...15 NAS 1638: class 9
- 5....420 mm²/s
Electrical
- DC
- -10 .... +10%
- Continuous, with ambient temperature ≤ 50°C (122°F)
- 150°C (302°F)
- See page before ms
- H
- Low Voltage Directive LVD 73/23/EC (2006/95/EC), 2004/108/EC
- 12 V
- 13 V
- 24 V
- 27 V
- DC
- DC
- DC
- DC
- 36 W
- 36 W
- 36 W
- 36 W
- 3.0 A
- 2.77 A
- 1.53 A
- 1.32 A
1) Nominal
2) ± 7% at temperature 20°C (68°F)
For applications with different specifications consult us.
- 3.97 Ω
- 4.68 Ω
- 15.67 Ω
- 20.42 Ω
Characteristic curves
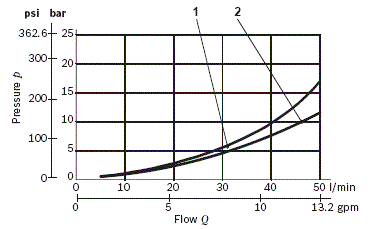
The graph is valid with either coil “a” or “b” energized.
Measured with hydraulic fluid ISO-VG32 at 45° ±5 °C
(113° ±9 °F); ambient temperature 20 °C (68 °F).
Performance limits
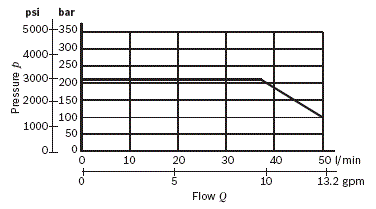
The performance limits are the same for both P > A or B, and T > A or B.
External dimensions and fittings
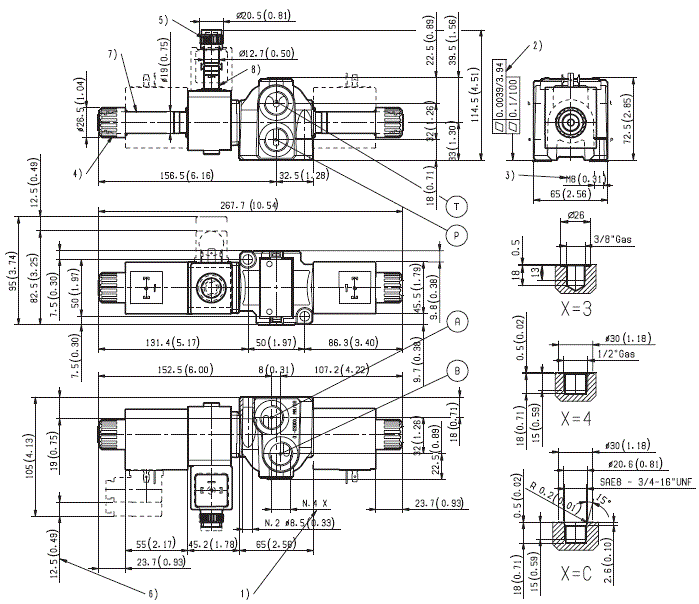
Electric connection
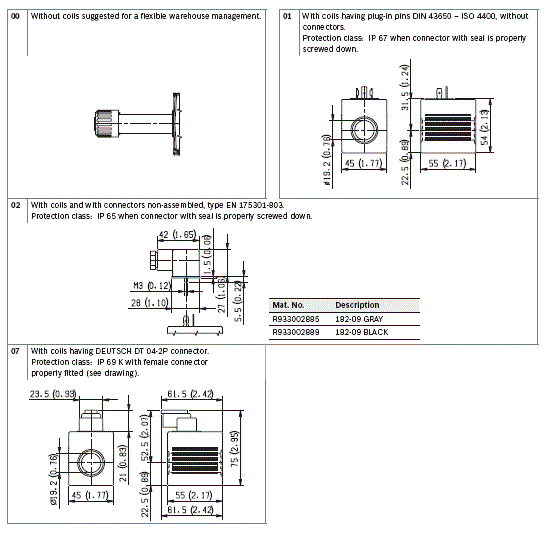