ELECTRONIC CONTROL OF HYDRAULIC SYSTEMS
As mobile equipment becomes more technologically sophisticated, the need for electronic control of hydraulic systems is growing.
Electronic components have become more reliable and rugged. They can now withstand the harsh environmental conditions required for mobile equipment applications.
Sophisticated electronic controllers normally supply only low power control signals. Amplification of the control signal is usually required to actuate solenoid-operated hydraulic valves. Electronic controllers that are designed for hydraulic applications will normally include the required amplification functions.
Why Pulse Width Modulation (PWM)?
When voltage is applied to a valve coil, the current flowing through it creates a magnetic field which provides the force to shift the valve’s spool or poppet. The input voltage divided by the resistance of the coil equals the current draw. This is very straightforward when used with on/off valves, but proportional valves are only useful if the spool position can be precisely controlled by varying the input current.
A simple potentiometer can be used to vary the resistance, which then varies the input current. This is an inefficient method of control, and is not practical when high currents are required. Also, when an infinitely variable DC signal is used to operate a proportional valve solenoid, the output transistor of the amplifier functions like a variable resistor. It drops the power supply voltage down to the level required by the solenoid coil at a particular time. The full coil current, which may be several amps, needs to pass through this output transistor. The result is that the transistor builds up heat which requires a large heat sink to dissipate.
Pulse Width Modulation (PWM) is a control technique which can overcome the problems described above. With PWM, the output transistor is used as an on/off switch, feeding the solenoid coil with a series of on/off pulses at a constant voltage. The pulses are set at a constant frequency, typically 400 to 5000+ Hz. The signal level is determined by varying the duration of the “on” pulses relative to the “off” pulses.
The advantage of this technique is that during the “off” pulse, the output transistor is not passing any current, and during the “on” pulse, there is virtually no voltage drop across the transistor and therefore very little heat is created. In practice, there will be a small voltage drop across the transistor during the “on” pulses, and it takes a finite amount of time to switch on and off, so a small amount of heat is created. However, the amount of heat is much smaller than would be produced by a conventional DC output signal.
PWM has become the standard for all valve amplifiers in order to reduce amplifier size and power waste. No modifications are required to the valve solenoid in order to use this technique. PWM is an efficient way to control current to a proportional valve coil. It allows the use of electronics for current regulation, dither, ramping, short circuit protection, and the elimination of deadband.
How PWM Works
A PWM signal is not constant, it is on for a period of time and off for a period of time, as shown below.
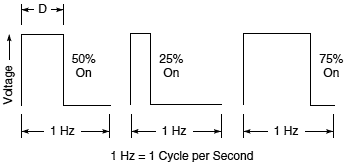
The duty cycle “D” refers to the “on” portion of the cycle. The duty cycle can be anywhere from 0 (signal always off) to 1 (signal always on). A 50% “D” results in a perfect square wave.
The PWM signal frequency can be low (100 to 400 Hz) or high (over 5000 Hz). High frequency PWM is more desirable because it produces a more constant ripple-free amperage output.
Coil Inductance
Inductance is the characteristic of a circuit that opposes the starting, stopping or changing of current flow. Inductance in an electrical system is similar to inertia in a mechanical system. Its effect is to introduce a time lag into the duty cycle wave form. In theory the wave form is perfectly rectangular, rising immediately when current is applied, and falling immediately when current is withdrawn. Because of the effects of inductance, the actual wave form rises and falls more gradually, as shown below.
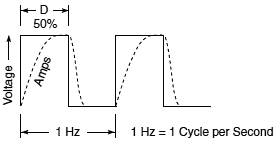
PWM Current Characteristics
At 25% signal, “D” is shorter than the time it takes the current to reach its maximum value. This results in reduced current output to the valve coil, and therefore a reduced hydraulic output from the valve. If the PWM frequency is low enough, the current will fall to zero during the off time. This is described as “discontinuous current,” illustrated below.
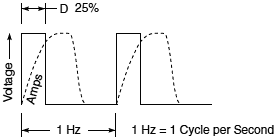
Dither (Current Ripple)
Stiction and hysteresis can make the behavior of a hydraulic proportional valve seem erratic and unpredictable.
Stiction keeps the valve spool from moving when input signal changes are small. When the signal finally becomes large enough to initiate movement, the spool will tend to overshoot the position required for accurate control.
Hysteresis is the tendency for the spool shift to be different depending on whether the change is increasing or decreasing, even when the control signal input value is identical.
Dither is a rapid, small movement of the spool around the desired position. It is intended to keep the spool moving to avoid stiction and average-out hysteresis. Dither amplitude must be large enough and the frequency slow enough for the spool to respond, and yet small and fast enough to avoid creating a noticeable pulsation in the hydraulic output of the valve.
Dither is caused by coil current “ripples” – current variations around the desired control signal value. Due to inertia, the valve spool will follow low frequency ripples better than it will follow high frequency ripples. The amplitude of the ripples determines if, or how far, the spool will move at a given frequency.
Low Frequency PWM
Low Frequency PWM, typically less than 400 Hz, generates dither (current ripple) as a by-product of the PWM process (illustrated below). The PWM frequency is low enough so that the current has time to decay before the next rise begins. The amount of dither (ripple) changes as the average coil current changes. Dither is maximum at 50% “D.” Dither decreases to zero at 0% and 100% “D.” This can result in too much dither at some current levels and not enough at others.
The dither current amplitude at a given average current is a function of coil inductance and PWM frequency. The inductance of a coil is largely a function of its rated voltage and wattage. A low wattage coil will usually have more inductance (thus less by-product dither for a given PWM frequency) than a high wattage coil.
Different valve designs will have differing responses to the same dither frequency and amplitude. Changing the PWM frequency will allow adjusting the dither, but the amplitude and frequency of the dither cannot be set independently as may be required by various valve designs.
High Frequency PWM
When the PWM frequency is high enough, typically above 5000 Hz, the coil current will be constant for all practical purposes, as shown below. No by-product dither will be produced by high frequency PWM.
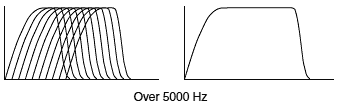
The advantage of using high frequency PWM is that dither can be generated separately and then superimposed on top of the output current, illustrated below. This allows the user to independently control the current level, as well as the dither frequency and amplitude. The dither will therefore be constant for any current level, and its frequency and amplitude can be set by the user to optimize the function of the particular hydraulic valve.

Ramps
Ramps are used to slow down the response of the valve driver to a changing command input. This results in a smooth transition when an abrupt change of the command input signal occurs. Ramps have no effect if the input signal change is slower than the ramp setting.
Ramps can be fixed or adjustable, symmetrical or independent, and single or dual. Adjustable ramps usually operate in the zero to eight second range and are controlled by a potentiometer. Single-side ramps are usually used in slow-shift controls where only acceleration is a concern.
Symmetrical ramps (shown immediately below) are controlled by a single potentiometer that adjusts the increasing and decreasing ramps identically.
Independent ramps (shown immediately below) have separate potentiometers for the increasing and decreasing sides, allowing acceleration and deceleration to be set independently of one another.
Dual-coil bi-directional valve drivers offer two independent ramps per coil, for a total of four independently controlled ramps, shown below.
Gain or I-Max.
The gain of an amplifier is the ratio of its large output signal (to the valve) to its small control input signal.
Gain = Output Signal ÷ Input Signal
The gain is usually adjusted by a potentiometer on the amplifier. This adjustment is usually called “I-Max.” Adjusting the I-Max. adjusts the amplifier gain. This can be used to adjust the maximum output of the amplifier (which controls the valve setting) for full input signal.
Enable / Disable
Some control/amplifiers incorporate an “Enable” function. This is a safety feature that requires a specific voltage to be present at the enable connection before the output of the controller will operate. Enable can be used for an emergency stop switch or other safety interlock device.
While it is possible to place an emergency stop switch in the power supply, this is not recommended because stored charges in capacitors can maintain the valve signal for a period of time after the switch is opened.
Deadband / I-Min.
Spool-type proportional valves will normally have a certain amount of spool overlap which produces deadband. For pressure and flow controls this deadband will occur at the start of spool movement. For directional valves the deadband will occur around the center position. Spool overlap reduces leakage in the null position and also provides a greater degree of safety in power failure or emergency stop situations. The effect of spool overlap requires that a certain minimum signal level has to be present at the solenoid coil before any noticeable result occurs in the system.
If this characteristic is undesirable, deadband can be eliminated or reduced (for pressure and flow controls) by setting a minimum current (I-Min.) on the controller/amplifier. When I-Min. is adjusted above the zero point, the valve spool will immediately jump to this setting when power is appled, eliminating the deadband. Please note that the I-Min. adjustment will affect the I-Max. setting, so it should always be set first.
When controlling directional valves using a multifunction/dual solenoid driver, the deadband elimination function is normally activated using a dip switch. The amount of deadband jump is typically factory-set, and is application-specific.
Current Feedback
When a current passes through a solenoid coil, heat is generated. This heat increases the resistance of the coil. For example, a coil may have a resistance of seven ohms at 20°C, and a resistance of nine ohms at 100°C. This increased resistance causes a reduction in coil power which results in a lower valve setting.
To compensate for temperature induced changes, some controller/amplifiers have a function known as “Current Feedback.” A current feedback resistor is added to the circuit in series with the solenoid coil. This allows the solenoid current to be proportional to the input signal voltage, and independent of the solenoid resistance. Power supply voltage must be sufficient to overcome the increased resist