
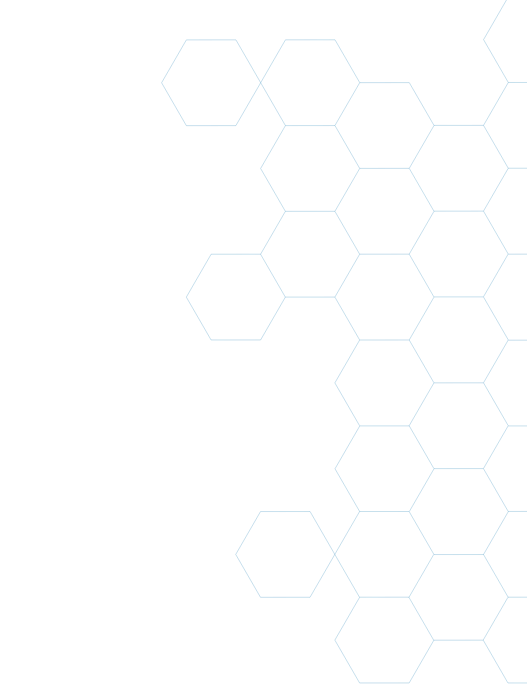
Compact Power Modules - DL Series
DL
Compact power modules DL series
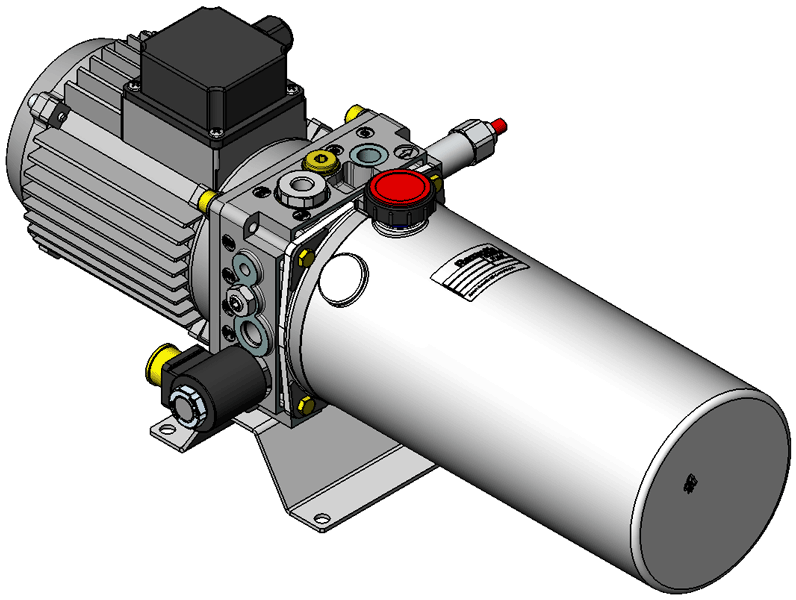
Ordering details for compact power modules for dock leveller with hinged lip (manifold code 66-67)
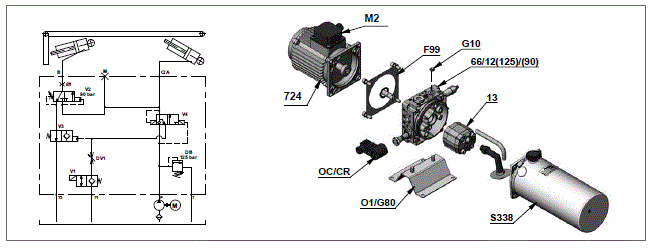
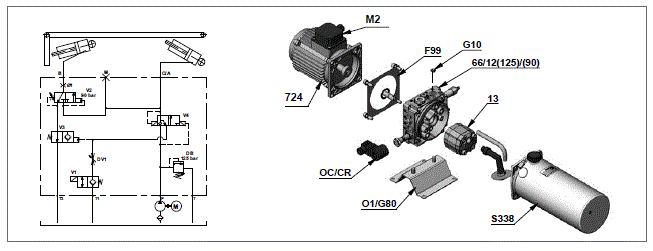
Example of Ordering Details
Ordering details for compact power modules for dock leveller with telescopic lip (manifold code 73)
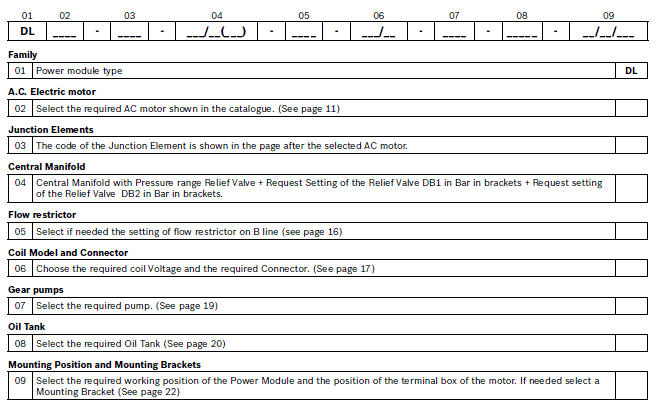
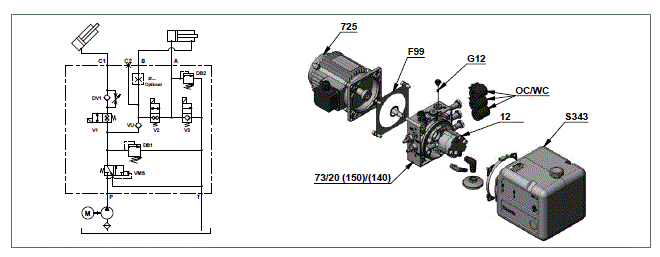
Example of Ordering Details
General Technical Data for Compact Power Module DL
Application description:
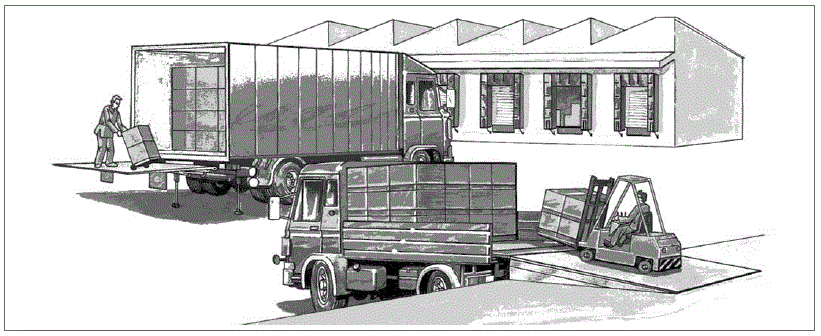
A Dock leveller is a structure which is typically fixed at the doors of the warehouse to load/unload goods. It’s used as a crossing bridge by Forklift, Transpallet etc, between the floor of the warehouse and the truck. (Picture 1)
Hydraulic system description:
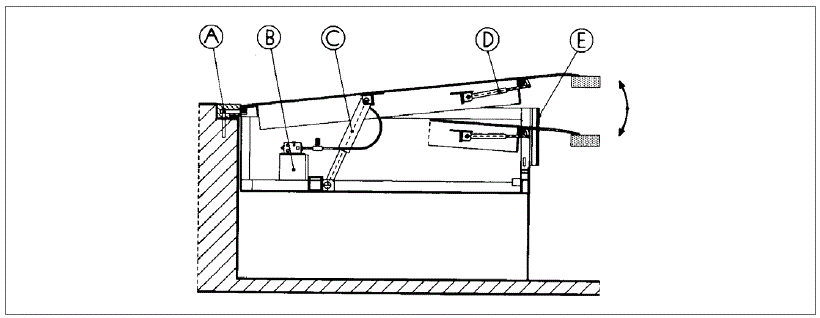
In a Dock leveller the hydraulic system is characterized by a main single acting cylinder C (in some case 2 single acting cylinders connect to the same ports of the compact power module) for the lifting function and a single acting cylinder to move the lip D in case of Dock leveller with a hinged lip (picture 2-3) or a double acting cylinder in case of Dock leveller with a telescopic lip. (Picture 4)
Picture 2 (typical Hydraulic Dock leveller scheme)
How the system works:
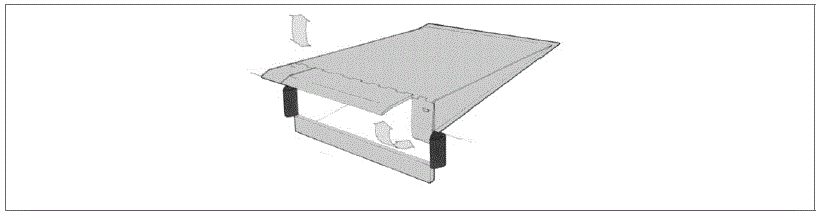
Hydraulic Dock leveller with Single acting cylinders hinged lip (Picture 3)
Lifting phase: By switching on the electric motor, the gear pump pushes oil into the system and with the raising of the pressure the V4 valve changes over giving the possibility for the oil to push the main lifting cylinder connected to the port C/A; The solenoid valve V1 must always be energized or the system doesn’t work.
When the main lifting cylinder arrives at the end of the run, the pressure increases and allows for the opening of the V2 sequence valve that starts to put oil into the hinged lip single acting cylinder connected to the port B; The opening speed is set by the dimension of the orifice Ø….
Lowering phase: By stopping the electric motor, the V4 valve changes over on to the normal position, so the oil goes to the return line, crossing the V1 and through the throttle valve DV1 which maintains a backpressure on the system that causes the changing over of the V3 valve that guarantees a backpressure on the lip single acting cylinder and for this reason the lip remains lifted while the main single acting cylinder lowers down. When the main singleacting cylinder stops lowering, leaning on the truck, the pressure on the system is out and automatically the V3 valve goes on the normal position, allowing the oil to run on the return line and allowing the lip to lean on to the track. The Dock leveller remains free to swing to compensate the differences on the truck level during the loading/unloading operations.
Closing phase: To close the Dock leveller you need to restart the motor by lifting the main cylinder (in consequence the lip cylinder is going to close with a setting speed set by the orifice Ø…).
When the lip is completely close the motor can be switched off and the Dock leveller returns to the normal position. The V1 solenoid valve normally is connected to the emergency push button of the system. Pushing the emergency button the V1 valve return in closed position keeping the cylinder in position.
Picture 3 (Hydraulic hinged lip Dock leveller)
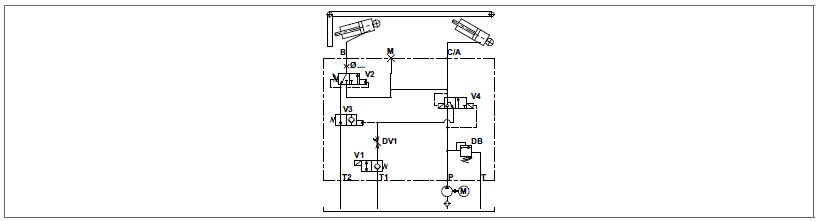
Scheme 1
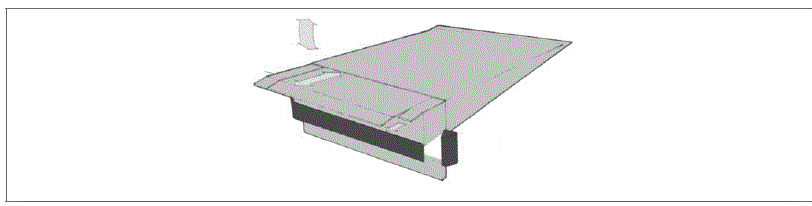
Picture 4 (Hydraulic telescopic lip Dock leveller)
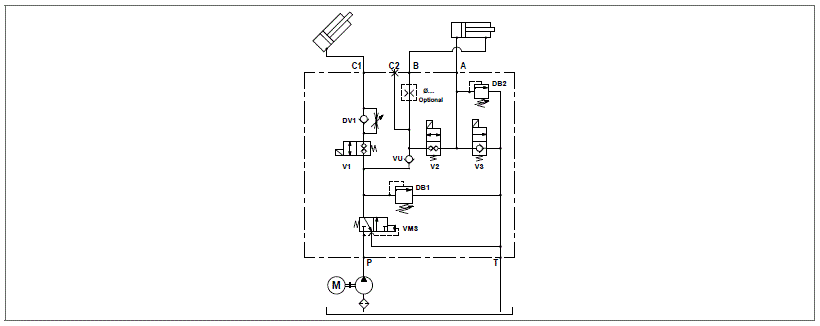
Hydraulic Dock leveller with double acting cylinder telescopic lip (Picture 4).
Opening phase: On the opening phase you need to switch on the electric motor energizing simultaneously the V1 (1) solenoid valve. The VMS valve changes over and the main cylinder connected to port C lifts: When the main cylinder arrives at the required position, we energize the V2 (2) solenoid valve and in consequence the telescopic lip double acting cylinder comes out in a regenerative mode between the A zone and B zone. When the telescopic lip arrives at the end of stroke the motor is switched off and all the solenoid valves are switched off too, so that the Dock leveller is completely open. The lip exit speed is controlled by the orifice Ø1.2 (optional).
Lowering phase: With the motor switched off the Dock leveller starts to lower itself energizing the V1 (1) solenoid valve which moves the main cylinder, which lowers down until it is leaning itself on the truck. The lowering speed is controlled by the STM12-VU valve.
The VM2 relief valve that is located on the double acting cylinder A line works as an antishock during the lip exit phase and also as protection of the same in case of an occasional bump as the truck stops.
Closing phase. To bring back the Dock leveller to the sleeping position, we need to repeat the opening phase to lift the Dock leveller from the truck and after to retract back the lip we need to energize the V3 (3) solenoid valve which puts the double acting chamber A on the return line.
Power module selection
Choose the circuit which meets your application requirements.
Take note of all dimensions resulting from the basic components chosen for your application.
NOTE: dimensions may vary slightly and should be confirmed by DCOC, if the assembly is to be installed in a space with narrow clearance.
The tank capacity and the tank dimensions need to be large enough to assure proper pump suction: there must always be a reserve of oil in the tank when all cylinders are fully extended and avoid overflow when cylinders are fully retracted.
The tank must be evaluated also for best separation of air from oil, and for settling down oil contamination. It should be placed in a space with, at least, natural ventilation and it should permit enough heat dissipation to prevent high fluid temperature.
Select the electric motor by evaluating the power needed and the motor compliance with the heat developed during the expected run time (or „duty cycle“).
Hydraulic fluid for compact power module
Mineral oil based hydraulic fluids suitable for hydraulic systems can be used; they should have physical lubricating and chemical properties as specified by:
MINERAL OIL BASED HYDRAULIC FLUIDS HL (DIN 51524 part 1)
MINERAL OIL BASED HYDRAULIC FLUIDS HL P(DIN 51524 part 2)
For use of environmentally friendly fluids please consult DCOC.
Fluid viscosity, Temperature range of the operating fluid, Ambient temperature
The fluid viscosity should remain within the range 10 to 300 cSt (centistokes); recommended 15 to 120 cSt .
Permissive cold start viscosity is maximum 2000 cSt .
The fluid temperature should remain within the range -15°C nd 80°C (5°F and 176°F).
Note: For compact power module with plastic tank the fluid temperature should remain within the range -15°C and 70°C (5°F and 158°F).
Ambient temperature -15°C +40°C (5°F and 104°F).
Fluid cleanliness requirements and maintenance
We recommend a cleanliness of the operating fluid according to ISO 4406 Class 20/18/15 or cleaner.
All components of the hydraulic circuit , including hoses and actuators, must be flushed and cleaned before assembling, because the compact power module has a suction filter only.
The hydraulic fluid should be replaced after the first 50 hours, and then every 1000 hours, or, at least, once a year.
Power module installation
The mounting position is basically unrestricted; just avoid installations that could compromise the pump suction, Typically in these applications the Compact Power Module is assembled in horizontal position. It is recommended to support the power module on vibration dampening blocks when the mounting structure is expected to vibrate.
Wiring and starting-up
The cable size and lenght from the power source to the electric motor should be selected in order to avoid voltage drop.
It is strictly forbidden to allow the backwards rotation of the pump even at the first starting: to prevent reverse rotation, the wiring polarities must be correctly connected. Caution: when energized, the surface temperature of the electric motor could reach temperature levels of 60-80°C (140-176°F): care should be taken to avoid any accidental contact of people with the motor surface.
A.C. Motors
The tolerances on the nominal voltage are:
Single phase motor: 230V +/-5% - Three phase motor: 230-400V +/-10%.
Protection degree : IP54 (protection against dust and water splash).
Insulation class: F (155°C) (311°F).
All motors are aluminum alloy die cast without painting.
Central Manifolds
The Central Manifolds shown in the catalogue are made in die cast aluminium alloy or extruded aluminum alloy AL 2011 (Al-Cu5.5Pb0.4Bi0.4 UNI 9002/5).. The validation of the Central Manifolds follows a lifetest with 250 bar (3625 psi) pulsed pressure repeated for 300.000 cycles.
Built-in valves
The valves used in the central manifolds are manufactured using steel with high mechanical strength. Surface treatments protect the exposed parts to the external environment. Standard seals are NBR (BUNA-N) with backup rings in PTFE. The cartridge valves with “leak proof seat design” have an average leakage of 10-15 drops/ minute (< 1 cm3/minute (0.06 in3/min)) at the maximum pressure using fluid ISO VG46 at 40°C (104°F). The validation of the cartridge valves follows a life-test at pulsed maximum pressure (indicated for each valve) repeated for 500.000 cycles.
All the solenoid cartridge valves are fitted with protective O-Rings installed between the pole tube and the coil. These O-Rings protect the internal parts from condensation and contaminants , which could cause malfunction.
All the solenoid cartridge valves are designed for operating in D.C..
Power supply in A.C. requires a connector with bridge rectifier included.
External Gear Pumps
DCOC offers a wide range of External Gear Pumps to cover different kind of applications. The standard version are suitable for the biggest part of applications. All the pumps are pressure compensated to guarantee the best efficiency.
Oil Tanks
In this catalogue you will find a wide selection of steel and plastic tanks available as a standard product. Steel tanks have Black paint finish and are suitable for operating temperature range -15°C / +80°C (5°F / 176°F). Plastic tanks are obtained in one piece in order to avoid welded parts that are weak points at extreme temperature and vibrations. Plastic tanks are suitable for operating temperature range -15°C / +70°C (5°F / 158°F).
NOTE: even if the plastic tank mounting system is designed to avoid oil leakage the tank must be securely anchored when fitted in mobile equipment and when subject to shocks and heavy vibrations. Please check that the anchorages do not stress or deform the tank.
European machine directive 2006/42/CE
According to the Machine Directive2006/42/CE, a complete power module, as described in paragraph 15 and made available to the European market, enters into the definition of „partly completed machinery“.
Instead, the power module subassemblies (motor, pump, reservoir, central manifold,...), when not assembled into a complete power pack, are considered „components“ which can be employed in a „machinery“ or a „partly completed machinery“. In this case, the DCOC components and subassemblies must be fitted in compliance with all the relevant technical data sheet applicable to the product, and shall not be operated, adjusted or disassembled before the complete machinery where they are incorporated has been declared to be in compliance with the Machine Directive 2006/42/CE.
NOTE:All the components shown in the catalogue ARE NOT suitable for use in potentially explosive atmosphere.
Technical information
Below you will find the most common equations used in hydraulics:
A.C. Electric Motor Compact Mounting Style for Power Module Type DL
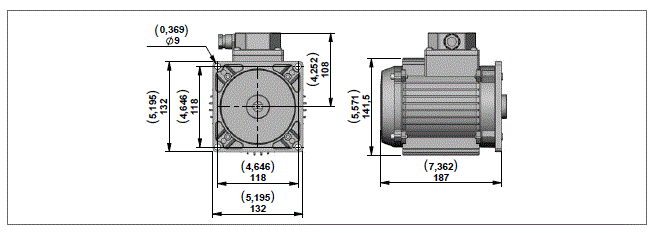
IP54 Size IEC 71
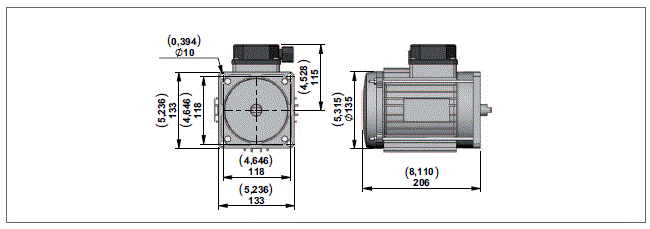
IP54 Size IEC 80
The motors shown in these tables are a selection of our range.
In case of needs of different technical characteristics PLEASE CONTACT OUR SALES DEPARTEMENT.
F99
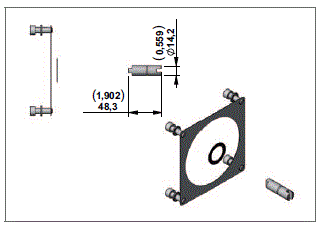
TR08
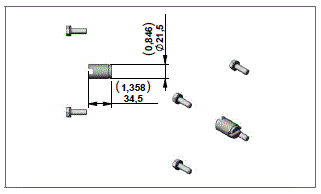
Junction Elements for manifolds MT
NOTE: The electric motors shown in this pages are delivered by different certified suppliers. This means the indicated dimensions could change a little, depending on which manufacturer will be assembled. On the CPM the choice of the manufacturer is based on our stock availability.
Central Manifold DL
66
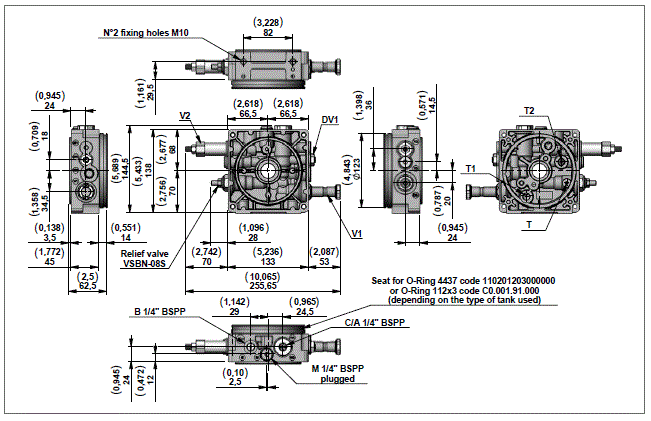
Manifold Hydraulic Diagram
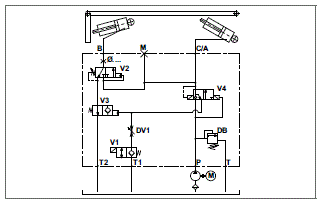
67
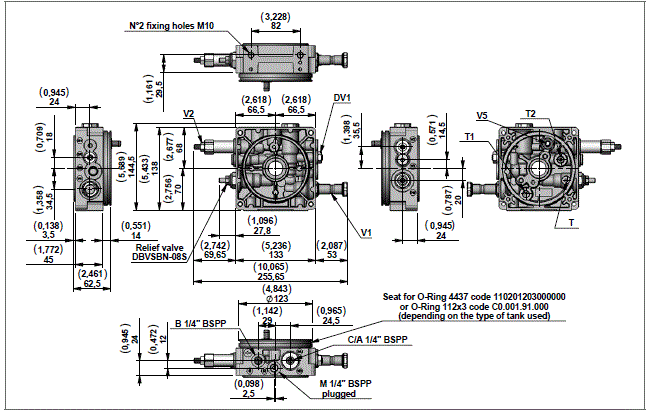
Manifold Hydraulic Diagram
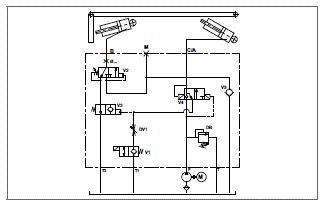
73
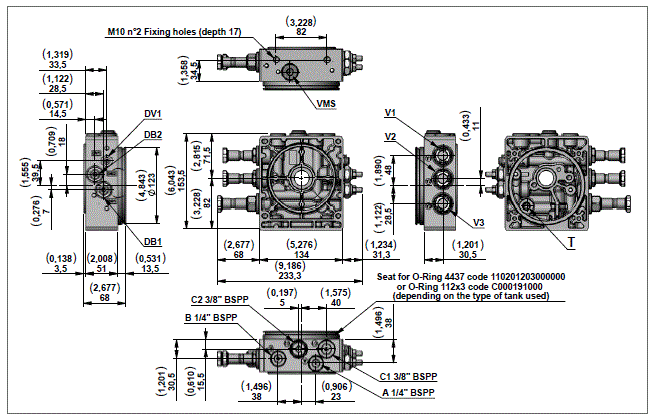
Manifold Hydraulic Diagram
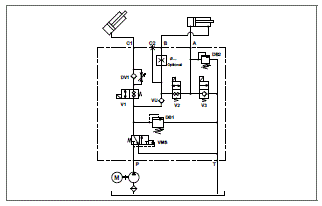
Flow Restrictor
Flow restrictor for manifold code 66-67
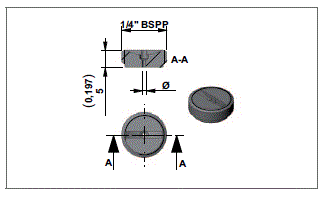
Flow restrictor for manifold code 73
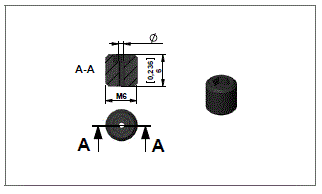
Coil
Technical Data
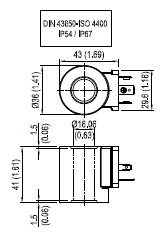
Weight: 0.18 kg (0.40 lbs)
Power: 20 W
Heat insulation Class H: 180°C (356°F)
Ambient temperature range: -30/+90°C (-22/+194°F)
Further performance limits in terms of temperature and voltage fluctuations: please refer to data sheet of the solenoid valve where D36 coil is mounted.
Coils D36 DIN 43650
Connectors
CONNECTOR IP67 - EN175000 (DIN 4350-A) / ISO 4400
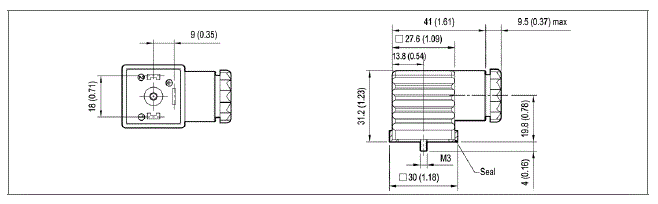
Standard Circuit

Circuit with VDR + Wave Rectifier

Gear Pumps
Gear Pumps Group 1
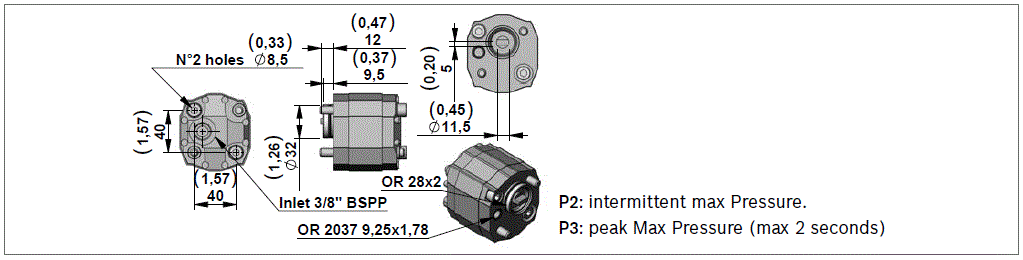
Oil Tanks for DL
Technical Data for Plastic Tanks

For this tanks is necessary to use the O-RING Ø112x3 code: C000191000 R-Number: R932000190


Assembly Kit for Plastic Tank - DL

Technical Data for steel Tanks

Mounting position


Terminal Box Position for A.C. Motors




Mounting Brackets



